Dough133 Electronics Design
Posted on March 17, 2024 • 11 min read • 2,228 wordsThis is a follow-up to the post introducing the Dough133 project. It describes the development and eventual design of the electronics that power the Dough133 project.
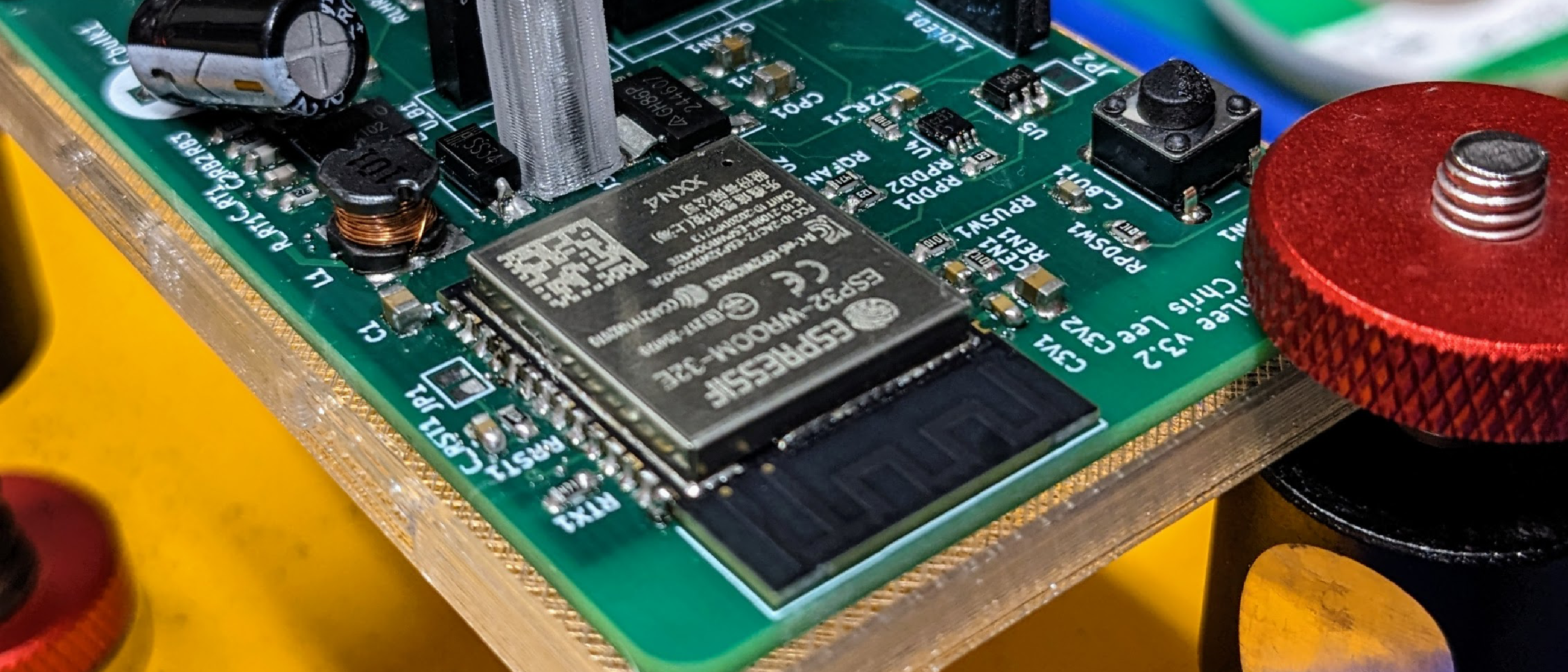
Introduction
This is a follow up to the post on Dough133, a heated enclosure for fermenting and proofing sourdough bread. This post focuses on the design of the custom controller board in the EBox that is mounted on the side of the cooler. In particular, it covers the selection of electronic components and the design of the printed circuit board.
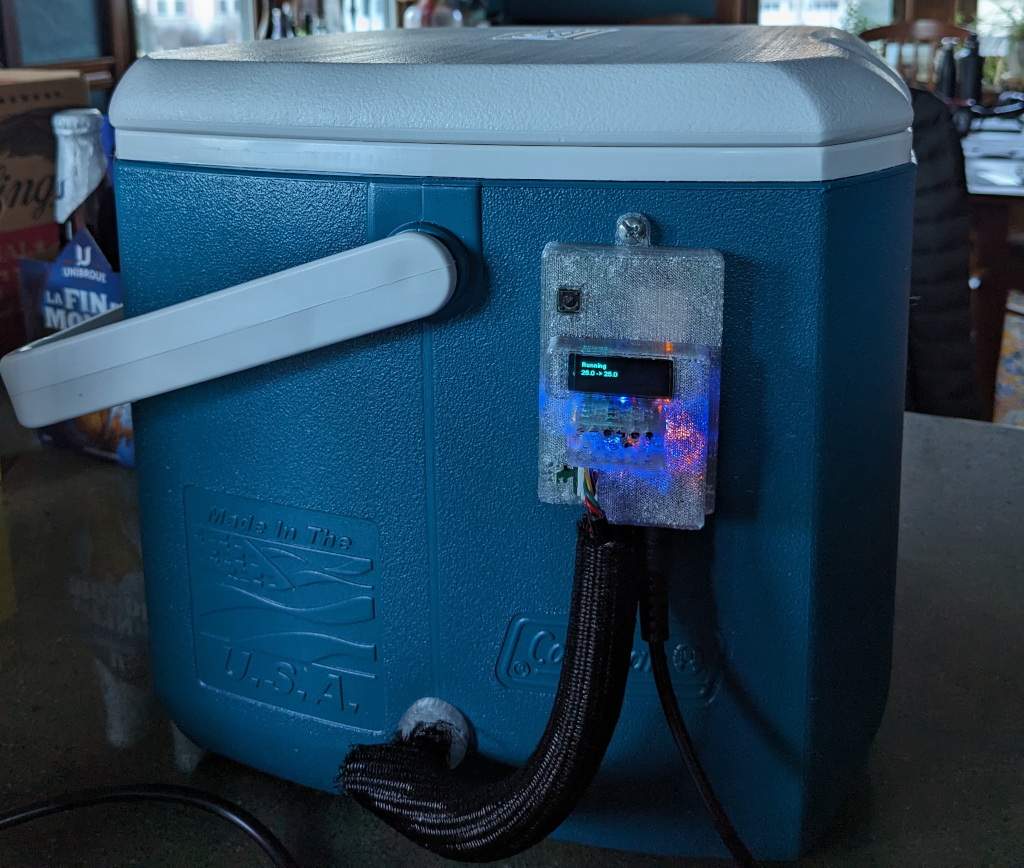
Heater and fan control
It is not really necessary to control the temperature of the Dough133 enclosure with extreme precision. As long as we have good sensors and control hardware, however, precise control is far more satisfying. To closely control the temperature, we need incremental control over the power provided to the heater. We cannot just run the heater like a steam furnace: at either full power or no power. A common way to gain this kind of incremental control is to use a MOSFET1, a component that allows quickly switching power between full-on and full-off, in combination with pulse-width modulation (PWM)2. PWM is performed by rapidly cycling the power on and off, but varying the proportion of time it is on verses off. This way we can precisely control the proportion of total available power that is provided to the heater.
Fan power control uses the same hardware but is controlled more simply, without PWM. The MOSFET is just used as a switch: setting the fan full-on when heat control is active, and full-off 90 seconds after heat control stops. This delay helps ensure the heater coils are cooled.
A flyback diode3 is used alongside each MOSFET.
A diode is a component which allows current to flow in one direction but not the other.
The figure below is a circuit diagram of a simple circuit with an inductance
and
a flyback diode
.
The resistor
represents the resistance of the inductor’s windings
Microprocessor
Earlier versions of the system were controlled using a Wemos Mini microcontroller, powered
by the ESP82664.
Power
The heater and fan both require 12V power.
The main power supply for the device is a 12V A/C adapter6 often used with
LED light banks.
The PCB incorporates a buck converter7 to efficiently convert the 12V
power to 5V.
This is a BD90610UEFJ-C8.
5V power is supplied to the OLED and enclosure’s SHTC3 module.
An LDO voltage regulator9 converts 5V to 3.3V.
The microcontroller and most other components use 3.3V power.
Safety circuit
In earlier versions of the system, I experienced a couple incidents where the microcontroller locked-up, and full unregulated power was sent to the heater. The PTC heater has an internal mechanism to limit its maximum temperature for safety, but the inside of the cooler quickly reached around 50°C (120°F) and stayed there until power to the system was shut-off. I don’t know why the microcontroller stopped running. My guess is that maybe the connection to the temperature sensor was poor, and software locked-up upon failing to read from it.
Whatever the reason, I wanted to make sure heater power would be cut-off if the microcontroller was not functioning properly. I thought a good approach was to require a “heartbeat signal” at a certain rate from the microcontroller. This is a digital output pin on the microprocessor which the software must toggle on and off to demonstrate it is running as designed. If the digital output stops, staying either high or low, then power to the heater must stop. With some googling, I found this forum post10 which explained that what I wanted was a “missing pulse detector” circuit. I incorporated a circuit using a SN74LVC1G123D Monostable Multivibrator11 IC which keeps its output high if pulses arrive at at least 100Hz. The circuit is an example application from the IC’s data sheet.11
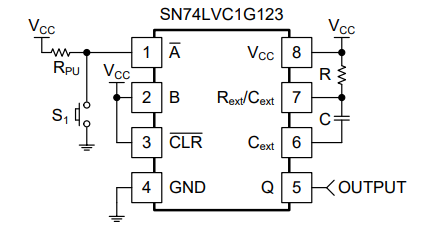
The timing diagram below from the data sheet indicates that if we have
,
a resistor with value
, and use a capacitor of
, then the
circuit should produce an output pulse with a duration
after each rising edge (a signal transitioning from low to high) is seen on its input.
If we provide an input signal of more than , these output pulses will run together and the output just stays high. If the input pulses stop and the signal stays locked high or low, then the output will go low in and stay there.
DHTR
is transmitted to the MOSFET via QHTR
only if rising edges
also arrive from output pin GPIO19
of the ESP325 microprocessor at a high enough rate.
If the microprocessor locks up or software is not running properly to generate the
heartbeat signal, power to the heater is quickly cut-off.
It worked!
I tested with a 50Hz input and saw a 50% duty cycle on the output.
That demonstrates a 10 msec high output on each rising edge, as expected,
followed by a 10 msec low output.
PCB design
This is one of the first PCBs I have designed. I’m learning about PCB design by iterating my designs and reading blogs and following some YouTube channels, but I’m self-taught and likely am doing some basic things wrong. So take my design with a grain of salt, defer to the real experts, and please post suggestions if you have them. That said, my boards do basically work, so that is something at least.
Design evolution
Here is the initial breadboard circuit I built while learning how to control the heater using PWM.
This used a Wemos D1 Mini clone microprocessor module, based on the ESP8266, for control.
“Modern” versions
My later PCB versions are based on the newer ESP32 microprocessor, and mostly use surface-mount components. The buck converter and LDO voltage regulator are part of the PCB, along with the safety circuit.
Here is a map of the component layout on a recent PCB.
The side-connector is a way to power and communicate with the board,
for programming and debugging via a serial monitor, without incorporating a
USB-to-serial chip and related components directly on the board.
I built a separate device which can attach to any board with this edge connector
and interface with USB.
Here is a view of the assembled PCB.
MOSFETs and heat
As an electronics newbie, one thing I am uncertain about is how to handle heat from the MOSFETS, which are the two large components sticking up from the middle of the board. I attached these via DuPont headers to make them easy to replace, and which somewhat thermally isolates them from the rest of the board. The heater’s MOSFET gets hot to the touch when the heater is at full power. However, the enclosure gets up to temperature quickly, and then the power sent to the heater is quickly reduced, so the MOSFET isn’t this hot for very long.
I could potentially attach a heat sink to the MOSFETs, or I could attach them to a large metal object to drain heat if one was nearby. Nearly everything near the EBox is plastic, however. For now, I just designed the EBox with air holes around the MOSFETs for cooling and this seems to be OK.
Problems
There are two main problems with the current board. The first is that the onboard SHTC3 sensor is not talking to the microprocessor. I might have done a poor job soldering the tiny component to the PCB (it is tiny), it could be a software problem, or it might be due to some problem with the PCB design. I’ll try to assemble the next version of the board and try again before attempting further debugging.
The second problem was the failure of a small capacitor on one board.
This was a small 0805 capacitor near the input of the boost converter IC.
I think I was using a component with appropriate specifications, but I could have
done something wrong.
This was also a cheap component from a big generic assortment ordered from AliExpress,
rather than from a more traceable source like Digikey.
I identified the failed component using my IR camera: the short across the component
caused it to get much hotter than the rest of the board.
Upon replacing the capacitor, the board worked again.
Conclusion
I’m not an electrical engineer, so I expect there are problems with this design easily noticed by the non-novice, or at least obvious ways to improve it. I’m still learning: please let me know what I could do better! Nevertheless, the system basically works as intended and it has been a fun learning experience to iterate through the design a few times. I plan to put my KiCAD files online at some point for others to use and/or critique.
References
The metal–oxide–semiconductor field-effect transistor (MOSFET) has the ability to change conductivity with the amount of applied voltage, and can be used for amplifying or switching electronic signals. Wikipedia. ↩︎
Pulse-width modulation (PWM) is a method of representing a signal as a rectangular wave with a varying duty cycle (ratio of “on” to “off”) Wikipedia. ↩︎
A flyback diode is any diode connected across an inductor used to eliminate flyback, which is the sudden voltage spike seen across an inductive load when its supply current is suddenly reduced or interrupted. It is used in circuits in which inductive loads are controlled by switches, and in switching power supplies and inverters. Wikipedia. ↩︎
ESP8266: a low-cost WiFi microchip, with built-in TCP/IP networking software, and microcontroller capability, produced by Espressif Systems. ↩︎
ESP32: a family of microcontrollers made by Espressif Systems. A successor to the ESP8266 microcontroller. ↩︎ ↩︎
A buck converter is a DC-to-DC converter which decreases voltage, while increasing current, from its input (supply) to its output (load). It is a class of switched-mode power supply. ( Wikipedia). ↩︎
A low-dropout regulator (LDO regulator) is a DC linear voltage regulator that can operate even when the supply voltage is very close to the output voltage ( Wikipedia). ↩︎
Missing pulse circuit found at this forum post. ↩︎
SN74LVC1G123D Monostable Multivibrator IC ( Digikey, data sheet). ↩︎ ↩︎
JLCPCB is the company from which I ordered circuit-boards designed with KiCAD. ↩︎
Through-hole technology is a manufacturing scheme in which leads on the components are inserted through holes drilled in printed circuit boards (PCB) and soldered to pads on the opposite side. Wikipedia ↩︎